3 Reasons Why You Should Use Oil-free Motors in the Food Industry
In food production, every component in your production line must meet the highest sanitary standards—including your motors. Traditional oil-lubricated motors come with hidden risks: they can leak, require extensive maintenance, and waste energy. Oil-free motors eliminate these concerns, offering a safer, more efficient, and more reliable alternative.
Yet, many machine builders hesitate to make the switch. Why? Because they’re unaware of the risks of oil-lubricated motors or assume that food-grade lubricants solve the problem. Let’s break down why oil-free drum motors are the smarter choice.
Written by Justin P. Caris, NGI DriveTech
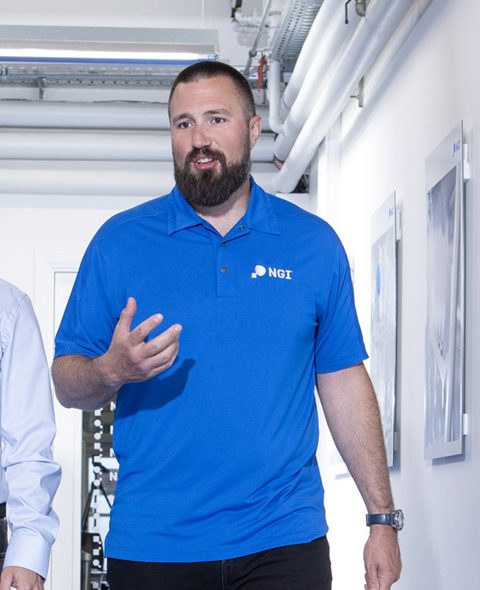