High performance without compromise: Why size is not an obstacle to performance in drum motors
In the world of industrial operations, efficiency, reliability, and performance are the cornerstones of any successful operation. Fitting conveyor systems or other machinery into existing production layouts can oftentimes lead to challenges with tight installation spaces. Traditional motors and gearboxes can eat up valuable space and complicate factory design. So the question arises: can compact solutions deliver the same level of power and performance as their larger counterparts? When it comes to drum motors, the answer is a resounding yes.
Written by Michael van Meegen, NGI DriveTech
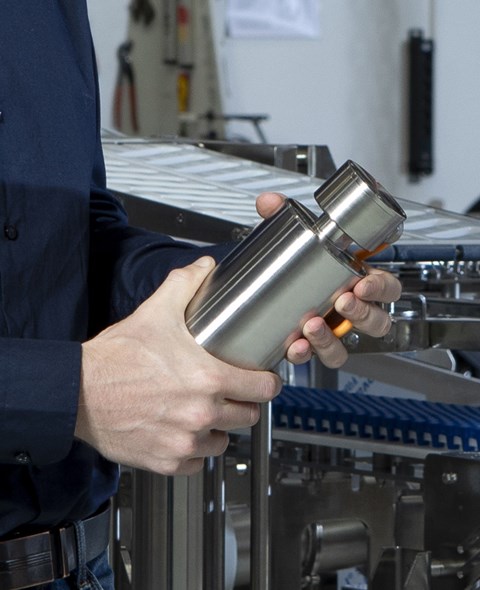