Why Choose Drum Motors over Gear Motors for Your Conveyor Systems?
Selecting the right motor for conveyor systems in the food processing industry is critical. This article dives into the differences between drum motors and external gear motors, focusing on design, ease of assembly, components needed, and energy efficiency.
Written by Justin P. Caris, NGI DriveTech
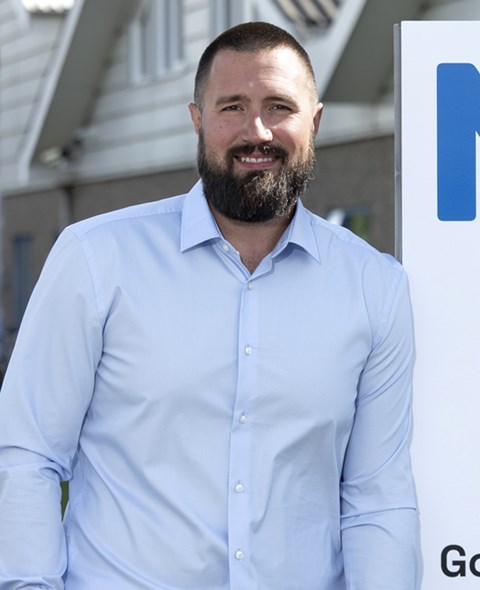